Ellipse: Do you know the orbit of planets, moon, comets, and other heavenly bodies are elliptical? Mathematics defines an ellipse as a plane curve surrounding...
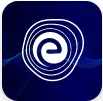
Ellipse: Definition, Properties, Applications, Equation, Formulas
April 14, 2025Ores found on the earth contains many impurities like sand, rocks, and grit in them, which are collectively known as “Gangue”. The concentration of ore is a method of removing gangue particles or other impurities in order to purify the ore. This process is also called Ore-dressing and benefaction. It is a very crucial step to obtain a pure metal from ore and to extract the metal.
Ore concentration is the chemical process of eliminating impurities like sand, rocks, silt, grit etc. from the ore to extract the metals in their pure form. In other words, it is the method of separating ore from the gangue, as the gangue or matrix particles are the valueless substances that are of no use. Both physical and chemical means can be used for the separation of ores. The purified ore obtained after the completion of the ore concentration is called concentrate.
Ore is defined as a solid substance (like a rock) that contains minerals or a mixture of minerals, from which the metal can be extracted by a series of methods like the concentration, isolation and refining.
Ores can be mainly classified into four types:
Ores found in the earth’s ground surface contains unwanted earthy materials like rocks, sand, silt, and other impurities colloquially termed as gangue. Concentration is basically the separation of something useful out of the impure substances. Thus, we can actually extract and refine metals through concentration of ore from such impurities,. We can use various physical and chemical processes to concentrate or separate ore from the gangue matrix.
The physical methods for the ore concentration include traditional handpicking, hydraulic washing, froth floatation, and magnetic separation.
(ii) Wilfley table: The other method of gravity separation is the Wilfley table. It is a wooden table having a slanting floor with riffles or grooves or cleats fixed on it.
The pulverized ore is placed on the trays provided at one end of the table, and a stream of water under pressure is passed over it. Thus, a rocking motion is given to the table. The lighter gangue particles are carried away by the stream of water while the heavy ore particles get deposited in the grooves. The ore particles deposited in the groove move towards one side of the table due to the rocking motion given to the table and are finally collected.
This method is used when the ore particles are heavier than the earthy or rocky gangue particles. This method is usually concentrated by the oxide ores iron (haematite), tin (Tin stone) and native ores of \({\rm{Au,}}\,{\rm{Ag,}}\) etc.
f. Electromagnetic separation: This method of concentration is employed when either the ore or the impurities associated with it are magnetic in nature. For example, chromite, \(\left( {{\text{FeO}}{\text{.C}}{{\text{r}}_{\text{2}}}{{\text{O}}_{\text{3}}}{\text{=FeC}}{{\text{r}}_{\text{2}}}{{\text{O}}_{\text{4}}}} \right)\) an ore of chromium, magnetite \(\left({{\text{F}}{{\text{e}}_{\text{3}}}{{\text{O}}_{\text{4}}}} \right){\text{-}}\) an ore of iron and pyrolusite \(\left({{\text{Mn}}{{\text{O}}_{\text{2}}}} \right){\text{-}}\) an ore of manganese being magnetic in nature, are separated from non-magnetic siliceous gangue by this method. Similarly, tinstone or cassiterite, an ore of tin being non-magnetic, can be separated from magnetic impurities like those of tungstates of iron and manganese, which are generally associated with this method.
In this method, the powdered ore is dropped over a conveyor belt moving around two rollers – one of which has an electromagnet in it. As the ore particles roll over the belt, the magnetic particles are attracted by the magnetic roller. As a result, two heaps are formed separately. The heap collected below the magnetic roller contains the magnetic particles, while the heap formed away from the magnetic roller contains the non-magnetic impurities. In the case of tinstone, the tungstate being magnetic fall in a heap under the magnetic roller while the ore particles that is \({\text{Sn}}{{\text{O}}_{\text{2}}}\) fall in a separate heap away from the magnetic roller.
g. Electrostatic separation: This method is used for the concentration/ separation of ores, which are good conductors of electricity, while impurities are poor conductors of electricity. The method is based upon the principle that when an electrostatic field is applied, the ore particles, which are good conductors of electricity, get electrically charged and hence are repelled by the electrodes having the same charge and thus are thrown away. This method is used for the concentration /separation of \({\text{PbS}}\) and \({\text{ZnS}}\) ores occurring together in nature. The mixture of ores is powdered and dropped over a roller subjected to an electrostatic field. \({\text{PbS}}\) being a good conductor, immediately gets charged and thrown away from the roller, whereas \({\text{ZnS}}\) is a poor conductor, does not get charged and falls vertically from the roller.
h. Froth floatation process: This process is commonly used for sulphide ores and is based upon different wetting characteristics of ore and gangue particles. The finely powdered ore is mixed with water, pine oil (frother) and ethyl xanthate or potassium ethyl xanthate(collector) in a big tank. Then, the whole mixture is agitated with air. The ore particles wetted with oil come in the froth and are taken off, while impurities wetted with water settle at the bottom.
The chemical methods include calcination, roasting and leaching for the concentration of ore.
It is the chemical method of separating carbonate or hydrated oxide ores.
It is a process generally applicable for sulphide ores under the influence of heat and air. In roasting, the sulphide ore is heated at a temperature below the melting point. For example:
If the mineral to be concentrated consists of sulphides of two metals, then adjusting the proportion of oil to water is often possible to separate one sulphide from the other. Additional reagents called froth depressants to prevent one type of sulphide Ore particles from forming the froth with air bubbles. For example, sodium cyanide is used as a depressant to separate lead sulphide ore from zinc sulphide ore. It is because \({\text{NaCN}}\) forms a soluble zinc complex \({\text{N}}{{\text{a}}_{\text{2}}}\left[{{\text{Zn}}{{\left({{\text{CN}}} \right)}_{\text{4}}}} \right]\) which goes into the solution thereby preventing it from forming the froth. Under these conditions, only \({\text{PbS}}\) forms a froth and hence can be separated from \({\text{ZnS}}\) ore.
\({\text{4NaCN + ZnS}} \to {\text{N}}{{\text{a}}_{\text{2}}}\left[{{\text{Zn}}{{\left({{\text{CN}}} \right)}_{\text{4}}}} \right]{\text{ + N}}{{\text{a}}_{\text{2}}}{\text{S}}\)
The process of treating the powdered ore with a suitable reagent that can selectively dissolve the ore but not the impurities is known as leaching.
The bauxite ore contains aluminium in the form of \({\text{A}}{{\text{l}}_{\text{2}}}{{\text{O}}_{\text{3}}}\) along with \({\text{Si}}{{\text{O}}_2},\) iron oxides and titanium oxide as impurities. The powdered ore is heated with a concentrated solution of \({\text{NaOH}}\) at \({\text{473-523}}\,{\text{K}}\) and \(35-36\) bar pressure. As a result, alumina is leached out as Sodium aluminate and \({\text{Si}}{{\text{O}}_2}\) as sodium silicate leaving behind the impurities.
\({\text{A}}{{\text{l}}_{\text{2}}}{{\text{O}}_{\text{3}}}{\text{ + 2NaOH + 3}}{{\text{H}}_{\text{2}}}{\text{O}} \to {\text{2Na}}\left[{{\text{Al}}{{\left({{\text{OH}}} \right)}_{\text{4}}}} \right]\)
\({\text{Si}}{{\text{O}}_{\text{2}}}{\text{ + 2NaOH}} \to {\text{N}}{{\text{a}}_{\text{2}}}{\text{Si}}{{\text{O}}_{\text{3}}}{\text{ + }}{{\text{H}}_{\text{2}}}{\text{O}}\)
The resulting solution is filtered to remove the undissolved impurities. Then it is cooled, and its \({\text{pH}}\) is adjusted either by dilution or by neutralization with \({\text{C}}{{\text{O}}_2}\) when aluminium hydroxide gets precipitated. In this stage, the solution is seeded with freshly prepared samples of hydrated alumina to get it precipitated, leaving behind sodium silicate in the solution.
\({\text{2Na}}\left[{{\text{Al}}{{\left({{\text{OH}}} \right)}_{\text{4}}}} \right]{\text{ + C}}{{\text{O}}_{\text{2}}} \to {\text{A}}{{\text{l}}_{\text{2}}}{{\text{O}}_{\text{3}}}{\text{.x}}{{\text{H}}_{\text{2}}}{\text{O + 2NaHC}}{{\text{O}}_{\text{3}}}\)
The hydrated alumina is filtered, dried and heated to 1400 K temperature to give back pure \({\text{A}}{{\text{l}}_{\text{2}}}{{\text{O}}_{\text{3}}}{\text{.}}\)
\({\text{A}}{{\text{l}}_{\text{2}}}{{\text{O}}_{\text{3}}}{\text{.x}}{{\text{H}}_{\text{2}}}{\text{O}} \to {\text{A}}{{\text{l}}_{\text{2}}}{{\text{O}}_{\text{3}}}{\text{ + x}}{{\text{H}}_{\text{2}}}{\text{O}}\)
Some metals like gold and silver are extracted from their concentrated ores by leaching. They are dissolved in suitable reagents like acids or bases, leaving behind insoluble impurities. Then the metal is recovered from the solution by precipitation or crystallization. For example, Silver ore is leached with a dilute solution of sodium cyanide. As a result, silver dissolves, forming a complex sodium dicyanoargentate(I). This solution is further treated with scrap zinc to get the precipitate of silver.
\({\text{A}}{{\text{g}}_{\text{2}}}{\text{S + 4NaCN}} \to {\text{2Na}}\left[ {{\text{Ag}}{{\left( {{\text{CN}}} \right)}_{\text{2}}}} \right]{\text{ + N}}{{\text{a}}_{\text{2}}}{\text{S}}\)
\({\text{2Na}}\left[{{\text{Ag}}{{\left({{\text{CN}}} \right)}_{\text{2}}}} \right]{\text{ + Zn}} \to {\text{N}}{{\text{a}}_{\text{2}}}\left[{{\text{Zn}}{{\left({{\text{CN}}} \right)}_{\text{4}}}} \right]{\text{ + 2Ag}}\)
Similarly, native gold is leached with a potassium cyanide solution, and it is recovered from the solution by the addition of scrap zinc.
\({\text{4Au + 8KCN + }}{{\text{O}}_{\text{2}}}{\text{ + 2}}{{\text{H}}_{\text{2}}}{\text{O}} \to {\text{4K}}\left[{{\text{Au}}{{\left({{\text{CN}}} \right)}_{\text{2}}}} \right]{\text{ + 4KOH}}\)
\({\text{2K}}\left[{{\text{Ag}}{{\left( {{\text{CN}}} \right)}_{\text{2}}}} \right]{\text{ + Zn}} \to {{\text{K}}_{\text{2}}}\left[ {{\text{Zn}}{{\left( {{\text{CN}}} \right)}_{\text{4}}}} \right]{\text{ + Au}} \downarrow \)
All materials found on Earth are made up of chemical elements. Most elements found on Earth are metals and nonmetals. There are numerous ways to carry out the concentration of ores. The correct method is chosen based on the physical and chemical properties of the metal. This article discussed important procedures like hand-picking, hydraulic washing, magnetic separation, froth floatation method, and leaching processes for the concentration of the ores.
The commonly asked queries on the concentration of ores are answered here:
Ans: The removal of the gangue from the ore is known as concentration or dressing or beneficiation. There are numerous methods of concentration, and the methods are chosen based on the properties of the ore.
Ans: Froth flotation method is used for the concentration of sulphide ores. The method is based on the preferential wetting properties with the frothing agent and water. Example: Galena (PbS).
Ans: Sulphide ores are concentrated by the froth-flotation process. Only sulphide ores are concentrated by this method because pine oil selectively wets the sulphide ore and brings it to the froth.
Ans: The ores of noble metals like argentite, an ore of silver and bauxite, an ore of aluminium etc., are concentrated by leaching.
Ans: Gravity separation, also called hydraulic washing, is a method of separation based on the difference in the specific gravity of the metallic ore and gangue particles.
Ans: Concentration of ore means removal of impurities by physical or chemical methods. The impurities like sand, rocky materials, limestone, mica, etc., present in the ore are called gangue or matrix. Concentration is necessary as it is easy to extract a metal when the impurities are removed at the beginning.