Ellipse: Do you know the orbit of planets, moon, comets, and other heavenly bodies are elliptical? Mathematics defines an ellipse as a plane curve surrounding...
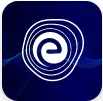
Ellipse: Definition, Properties, Applications, Equation, Formulas
April 14, 2025Ever wondered how the foil wrapped around our food keeps the food warm? Do you know which material is the foil made up of? What is the material of a soft drink can and aeroplane body? The answer is aluminium. Aluminium is the most abundant metal in the Earth’s crust (8.1%) but is rarely found uncombined in nature. It is usually found in minerals such as bauxite and cryolite. These minerals are aluminium silicates. There are various processes for the Extraction of Aluminium from natural minerals. In this article, we will learn the process of extraction of aluminium and see how we get such an amazing and versatile metal.
Aluminium is used in a huge variety of products including cans, foils, kitchen utensils, window frames, beer kegs and aeroplane parts. This is because of its particular properties. It has low density, is non-toxic, has high thermal conductivity, has excellent corrosion resistance and can be easily cast, machined and formed. It is also non-magnetic and non-sparking. It is the second most malleable metal and the sixth most ductile.
Aluminium is a soft, silvery-white, corrosion-resistant, and the most abundant metal in the earth’s crust. It makes up \(8\% \) of the earth’s crust, and it is the third most abundant element after oxygen and silicon. Bauxite ore \({\rm{(A}}{{\rm{l}}_{\rm{2}}}{{\rm{O}}_{\rm{3}}}{\rm{.x}}{{\rm{H}}_{\rm{2}}}{\rm{O)}}\) is the chief ore of aluminium, which is a mixture of hydrated aluminium oxide.
Aluminium is also found in gemstones such as garnet, topaz, and chrysoberyl.The chemical symbol of aluminium is Al. It belongs to group \({\rm{13}}\) and period \({\rm{3}}\) of the Modern Periodic Table. \({\rm{13}}\) electrons are distributed in \({\rm{13}}\) shells and have an electronic configuration of \({\rm{1}}{{\rm{s}}^{\rm{2}}}{\rm{2}}{{\rm{s}}^{\rm{2}}}{\rm{2}}{{\rm{p}}^{\rm{6}}}{\rm{3}}{{\rm{s}}^{\rm{2}}}{\rm{3}}{{\rm{p}}^{\rm{1}}}\) . It has an atomic mass of \(28.98\,{\rm{g/mol}}\).
Aluminium is a highly reactive metal and hence is not available in a state. Naturally, aluminium is found in the form of its oxide in its ores. The important ores of aluminium are:
Bauxite is the chief ore from which aluminium is extracted. It is formed from a reddish rock clay like material called laterite soil. It is most commonly found in tropical or subtropical regions. Bauxite is composed of aluminium oxide compounds (alumina), silica, iron oxides and titanium dioxide. Aluminium is obtained by the Electrolysis of Alumina. The concentration of the Bauxite ore into alumina is done by Bayer’s process. Alumina is then refined into pure aluminium metal through the Hall–Héroult electrolytic process.
Aluminium is too high in the electrochemical series (reactivity series) to be extracted from its ore using carbon reduction. The temperatures needed are too high that is not economical.
Instead, it is extracted by electrolysis. The ore is first converted into pure aluminium oxide by the Bayer Process, and this is then electrolyzed in a solution of molten cryolite – another aluminium compound. The aluminium oxide has too high a melting point to electrolyze on its own.
The Bauxite ore is crushed and pulverized, i.e. it is ground and made into a powder. Bauxite ore generally contains ferric oxide and silica as impurities. Ferric oxides are removed through magnetic separation.
To extract Aluminium from Bauxite, the ore needs to concentrate. Bauxite is purified to generate Aluminium Oxide or Alumina from which aluminium can be extracted. The conversion of Bauxite to Alumina is done by Bayer’s Process.
The Bayer Process, developed by Carl Josef Bayer. is the principal industrial means of refining bauxite to produce alumina (aluminium oxide). In this process, aluminium ore is treated with concentrated sodium hydroxide to form a soluble sodium aluminate. Sodium aluminate is filtered, and the filtrate on heating with water gives aluminium hydroxide. Aluminium hydroxide, on heating strongly with water, gives alumina. The steps followed in Baeyer’s process are –
a. The crushed and pulverized bauxite is treated with moderately concentrated sodium hydroxide solution (caustic soda) to produce a slurry (a watery suspension) containing very fine particles of ore.
b. The slurry is pumped into a digester which acts as a pressure cooker. In the digester, the temperature is maintained around \({140^ \circ }{\rm{C}}\) to \({240^ \circ }{\rm{C}}\); and pressure is kept at about 35 atmospheres. These conditions are maintained for a time ranging from half an hour to several hours. Additional caustic soda may be added to ensure that all aluminium-containing compounds are dissolved.
c. High pressures are necessary to keep the sodium hydroxide solution in the liquid state when temperatures rise above \({100^ \circ }{\rm{C}}.\) The higher the temperature, the higher the pressure needed.
d. With hot concentrated sodium hydroxide solution, aluminium oxide reacts to give a solution of sodium tetrahydroxoaluminate.
e. This treatment also dissolves silica, forming sodium silicate :
\(2\,{\rm{NaOH}}\,{\rm{ + Si}}{{\rm{O}}_{\rm{2}}} \to {\rm{N}}{{\rm{a}}_{\rm{2}}}{\rm{Si}}{{\rm{O}}_{\rm{3}}}{\rm{ + }}{{\rm{H}}_{\rm{2}}}{\rm{O}}\)
f. However, the other metal oxides present as an impurity in bauxite tend not to react with the sodium hydroxide solution and so remain unchanged. The slurry is pumped into a settling tank where the impurities that do not dissolve in the caustic soda settle to the bottom of the vessel.
g. All of these solids are separated from the sodium tetrahydroxoaluminate solution by filtration, commonly with a rotary sand trap. A flocculant such as starch is added to remove the fine particles. They form a “red mud”, which is just stored in huge lagoons.
a. The crystals formed settle to the bottom of the tank and are removed. These crystals are then transferred to rotary Kilns or fluid flash calciners. In these Kilns, aluminium hydroxide crystals are heated at a temperature of \(2,{000^ \circ }{\rm{F}}\)\((1,{100^ \circ }{\rm{C)}}\)to drive off the water molecules chemically bonded to the alumina molecules.
a. The crystals formed settle to the bottom of the tank and are removed. These crystals are then transferred to rotary Kilns or fluid flash calciners. In these Kilns, aluminium hydroxide crystals are heated at a temperature of \({2000^ \circ }{\rm{F}}\)\({\rm{(1,10}}{{\rm{0}}^ \circ }{\rm{C)}}\) to drive off the water molecules chemically bonded to the alumina molecules.
b. For bauxites having more than \(10\% \) silica as an impurity, the Bayer process becomes uneconomic because of the formation of insoluble sodium aluminium silicate, which reduces yield, so another process must be chosen.
Conversion of the aluminium oxide into aluminium by electrolysis:
The Hall–Héroult process is a major industrial process that involves the smelting of aluminium. It involves dissolving aluminium oxide (alumina) obtained from bauxite through Baeyer’s process. In this process, pure alumina is mixed with Calcium fluoride \(({\rm{Ca}}{{\rm{F}}_2})\) or Cryolite \(({\rm{N}}{{\rm{a}}_{\rm{3}}}{\rm{Al}}{{\rm{F}}_6})\). Elemental aluminium cannot be produced by the electrolysis of an aqueous aluminium salt because hydronium ions readily oxidize elemental aluminium.
The electrolysis process is carried forward as shown below-
The arrangement above consists of a steel vessel with carbon lining. The carbon lining acts as the cathode (negative electrode), and graphite rods act as an anode (positive electrode). The anodes are suspended by rods in the molten alumina-cryolite mixture.
On passing electricity through the cell, oxygen is formed at the anode. The oxygen so formed reacts with carbon anode to form carbon monoxide and carbon dioxide. The cell operates at a low voltage of about \(5 – 6\) volts but at huge currents of \(100,000\) amps or more. The heating effect of these large currents keeps the cell at a temperature of about \(1000{\,^ \circ }{\rm{C}}\).
The overall reaction is:
\(2{\text{A}}{{\text{l}}_2}{{\text{O}}_3} + 3{\text{C}} \to 4{\text{Al}} + 3{\text{C}}{{\text{O}}_2}\)
The electrolytic reactions are:
At the cathode:
\({\text{A}}{{\text{l}}^{3 + }} + 3{{\text{e}}^ – } \to {\text{Al}}\left({\text{I}} \right)\)
At the anode:
\({\text{C}}({\text{s}}) + {{\text{O}}^{2 – }} \to {\text{CO}}\left({\text{g}} \right) + 2{{\text{e}}^ – }\)
\({\text{C}}({\text{s}}) + 2{{\text{O}}^{2 – }} \to {\text{C}}{{\text{O}}_2}\left({\text{g}} \right) + 4{{\text{e}}^ – }\)
During the process of electrolysis,
Oxygen discharged at anode reacts with carbon anode to form carbon dioxide gas.
Aluminium is heavier than the cryolite mixture settles at the bottom of the tank, where it is siphoned out from time to time. To sustain the electrolytic process, alumina is fed into the pots at regular intervals to maintain a sufficient quantity of dissolved alumina in the bath. For each ton of aluminium produced, about \(430\,{\rm{kg}}\)of carbon is consumed. A continuous supply of anodes is manufactured at both smelters in dedicated carbon plants.
The theoretical minimum energy requirement for this process is \(6.23\,{\rm{kWh/(kg}}\,{\rm{of}}\,{\rm{Al)}}\)but the process commonly requires \(15.37\,{\rm{kWh}}\)
The molten aluminium is mixed with desired alloys to obtain specific characteristics. In the fabrication shops, the molten aluminium or aluminium alloys are remelted and cast. Molten aluminium may be further heated to remove oxides, impurities, and other active metals such as sodium and magnesium, before casting. Chlorine may also be bubbled through the molten aluminium to further remove impurities.
Red mud is the waste produced in Bayer’s process of bauxite’s digestion with sodium hydroxide. It has high calcium and sodium hydroxide content with a complex chemical composition. It is very caustic and possess a potential threat to environmental pollution. It finds its use is in ceramic production. Red mud dries into a fine powder that contains iron, aluminium, calcium, and sodium. It becomes hazardous when some extraction plants use this waste to produce aluminium oxides.
Aluminium is a lightweight, silver-white metal. In this article, we learnt about the various processes involved in the extraction of aluminium. We also learnt about Baeyer’s process and Hall Herault’s process employed in aluminium extraction and refining. We learnt about the various uses of aluminium in our day to day life.
Q.1. What is the significance of leaching in the extraction of aluminium?
Ans: Leaching is done to concentrate pure alumina from bauxite ore. This is done by Bayer’s process in which bauxite is treated with caustic soda followed by heating and calcinating aluminium hydroxide.
Q.2. Why is cryolite used in the extraction of aluminium?
Ans: Pure alumina has a very high melting point of \(2072\) degree Celsius. Extraction at such a high temperature is not feasible. Hence cryolite is used to lower the melting point of alumina and increase its electrical conductivity.
Q.3. Why is Aluminium extracted by electrolysis?
Ans: Aluminium ranks above carbon in the reactivity series of metals. Hence, is more reactive than carbon. Therefore, carbon cannot be used for reduction purposes. Extraction of compounds for reactive metals should take place through the electrolysis process.
Q.4. What is aluminium used for?
Ans: Aluminium has a wide variety of uses ranging from consumer goods to infrastructure. Kitchen cutleries, vehicle parts, cans, household electrical appliances, power transmission lines and ships are some of the uses of aluminium.
Q.5. What are the steps involved in the extraction of Aluminium from bauxite?
Ans: Following steps are involved in the extraction of Aluminium from bauxite-
1.The concentration of the ore through Bayer’s process(Leaching)
In this process, bauxite is treated with \({\rm{NaOH}}\) to form sodium aluminate, which further reduces with \({\rm{C}}{{\rm{O}}_2}\) and gives pure alumina. The reaction is as follows-
\({\text{A}}{{\text{l}}_2}{{\text{O}}_3} + 2{\text{NaOH}} + 3{{\text{H}}_2}{\text{O}} \to 2{\text{NaAl}}{({\text{OH}})_4}\)
\({\text{NaAl}}{({\text{OH}})_4} \to {\text{Al}}{({\text{OH}})_3} + {\text{NaOH}}\)
\(2{\text{Al}}{({\text{OH}})_3} \to {\text{A}}{{\text{l}}_2}{{\text{O}}_3} + 3{{\text{H}}_2}{\text{O}}\)
2. Electrolytic reduction of Alumina (Hall-Herault’s Process)
Electrolytic reduction of pure alumina takes place in an electrolytic cell where carbon lining acts as the cathode. Graphite rods that act as an anode are dipped in an electrolytic mixture of cryolite \({\rm{(N}}{{\rm{a}}_{\rm{3}}}{\rm{Al}}{{\rm{F}}_{\rm{6}}}{\rm{)}}\) Fluorspar \({\rm{(Ca}}{{\rm{F}}_2})\)and alumina. The reactions at each of the electrodes are as follows
The overall reaction is:
\(2{\text{A}}{{\text{l}}_2}{{\text{O}}_3} + 3{\text{C}} \to 4{\text{Al}} + 3{\text{C}}{{\text{O}}_2}\)
The electrolytic reactions are:
At the cathode:
\({\text{A}}{{\text{l}}^{3 + }} + 3{{\text{e}}^ – } \to {\text{Al}}\left({\text{I}} \right)\)
At the anode:
\({\text{C}}({\text{s}}) + {{\text{O}}^{2 – }} \to {\text{CO}}\left({\text{g}} \right) + 2{{\text{e}}^ – }\)
\({\text{C}}({\text{s}}) + 2{{\text{O}}^{2 – }} \to {\text{C}}{{\text{O}}_2}\left({\text{g}} \right) + 4{{\text{e}}^ – }\)
We hope this detailed article on the Extraction of Aluminum is helpful to you. If you have any queries, ping us through the comment box below and we will get back to you as soon as possible.