Ellipse: Do you know the orbit of planets, moon, comets, and other heavenly bodies are elliptical? Mathematics defines an ellipse as a plane curve surrounding...
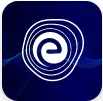
Ellipse: Definition, Properties, Applications, Equation, Formulas
April 14, 2025Polymerization is a process in which relatively small molecules, known as monomers, combine chemically to form a very large chainlike or network molecule known as a polymer. The monomer molecules may be identical, or they may represent two, three, or more different compounds. To learn more about the General Method of Polymerisation, read this article.
Polymerization is the process of joining together many small molecules called monomers to form a covalently bonded chain or network. Some chemical groups from each monomer may be lost during the polymerization process. This occurs during PET polyester polymerization.
Terephthalic acid \(\left( {{\rm{HOOC}} – {{\rm{C}}_6}{{\rm{H}}_4} – {\rm{COOH}}} \right)\) and ethylene glycol \(\left( {{\rm{HO}} – {\rm{C}}{{\rm{H}}_2} – {\rm{C}}{{\rm{H}}_2} – {\rm{OH}}} \right)\) are the monomers, but the repeating unit is \( – {\rm{OC}} – {{\rm{C}}_6}{{\rm{H}}_4} – {\rm{COO}} – {\rm{C}}{{\rm{H}}_2} – {\rm{C}}{{\rm{H}}_2} – {\rm{O}} – \), corresponding to the combination of the two monomers with the loss of one water molecule. A repeat unit or monomer residue is the distinct piece of each monomer that is incorporated into the polymer.
The major methods generally used for preparing polymers are:
Addition polymers are formed by combining monomers without removing any by-product molecules. Unsaturated compounds such as Alkenes, alkadienes, and their derivatives are used as monomers in addition to polymers. This polymerization process consists of a series of reactions, each of which consumes a reactive particle and produces another similar particle, resulting in a chain reaction.
The polymerization reaction is also known as chain polymerization or chain growth polymerization because it occurs in stages that lead to an increase in chain length, with each stage producing reactive intermediates for use in the next stage of chain growth. This type of polymerization reaction, like other chain reactions, involves an initiator, which could be a radical or a cation.
Depending upon the nature of the reactive species involved, the addition polymerization occurs by the following three mechanisms:
However, the radical addition polymerization is most common.
In the presence of a radical generating initiator (catalyst) such as benzoyl peroxide, acetyl peroxide, tert-butyl peroxide, and others, a variety of alkenes or dienes and their derivatives are polymerized. For example, heating or exposing a mixture of ethene and a small amount of benzoyl peroxide initiator to light results in the polymerization of ethene to polythene.
radical addition polymerization proceeds in three steps:
I. Chain initiation: The reaction begins with the addition of a radical formed by peroxide to the ethene double bond, resulting in the formation of a new and larger radical. This is known as the chain initiation step.
II. Chain propagation: The new radical reacts with a double bond of monomer to form a larger radical. The formed radical reacts with another alkene molecule to form a larger radical. This procedure is repeated until the radical is destroyed. These are known as propagation steps.
III. Chain termination: For termination of the long chain, these radicals can combine in different ways to form polythene. For example,
This is an addition polymer of ethene. These days, two types of polythenes, high-density polythene and low-density polythene, are produced using different polymerization conditions.
It is produced by the polymerization of ethene at high pressures ranging from \(1000\) to \(2000\) atmospheres and temperatures ranging from \(350\;{\rm{K}}\) to \(570\;{\rm{K}}\) in the presence of traces of dioxygen or a peroxide initiator (catalyst). The structure of low density polythene is highly branched. It is created by combining radicals and \({\rm{H}}\)- atom abstraction.
It is formed when addition polymerization of ethene takes place in a hydrocarbon solvent in the presence of catalyst like \({\left( {{{\rm{C}}_2}{{\rm{H}}_5}} \right)_3}{\rm{Al}}\) and \({\rm{TiC}}{{\rm{l}}_4}\) (Zeigler-Natta catalyst) at about \(333\;{\rm{K}}\) to \(343\;{\rm{K}}\) under a pressure of \(6 – 7\) atmosphere.
It is an additional polymer of tetrafluoroethene. It is made by heating tetrafluoroethene at high pressures with a radical or persulfate catalyst, (ammonium persulphate, \(\left. {{{\left( {{\rm{N}}{{\rm{H}}_4}} \right)}_2}\;{{\rm{S}}_2}{{\rm{O}}_8}} \right)\). It is a very tough and chemically inert material. It is heat resistant and resistant to corrosive reagents such as acids and bases. It is a poor electrical conductor.
It is a polymerized product of Vinyl cyanide (acrylonitrile). It is obtained by the addition polymerization of acrylonitrile in the presence of a peroxide catalyst. It is hard and contains high melting point substances. It is also known as acrilan or orlon.
The step growth polymerization, as the name implies, involves stepwise intermolecular condensation that occurs through a series of independent reactions. Each reaction involves a condensation process that results in the loss of a simple molecule such as \({\rm{N}}{{\rm{H}}_2},\,{{\rm{H}}_2}{\rm{O}},\,{\rm{HCl}}\), and so on.
This type of polymerization occurs if the monomer molecules have more than one similar or dissimilar functional group. Condensation polymerization results in the formation of polymers with a high molecular mass. Let us begin with two monomers \({\rm{A}}\) and \({\rm{B}}\) to demonstrate step growth polymerization in its most basic form.
The stepwise process of chain growth goes on. The stepwise growth can also take place in another manner.
The polymers formed by step growth polymerization are called step growth polymers. The condensation polymers like dacron, nylon, bakelite are formed by this type of polymerization.
These are polycondensation products of dicarboxylic acids and diols. This involves ester linkage.
For example,
I. Terylene It is obtained by the condensation reaction between ethylene glycol and terephthalic acid.
Characteristic and Uses of Polyester
It has very strong fibres. It is highly crease-resistant, long-lasting, and has a high moisture content.
II. Glyptal: It is a polymer of ethylene glycol and phthalic acid.
Uses of Glyptal
These polymers have amide linkage in the chain and are important examples of synthetic fibres termed as nylons. For example,
i. Nylon-6,6: Hexamethylenediamine and adipic acid are the monomer units of nylon-\(6,\,6\). It is prepared by the condensation of hexamethylenediamine with
acid under high pressure and high temperature.
Uses of Nylon-6,6
ii. Nylon-6: It has the monomer caprolactam which is obtained from cyclohexane. Caprolactam on heating with traces of water gives \( \in \)-amino caproic acid which is a mono-carboxylic amino acid containing six carbon atoms. This polymerized to give nylon-6.
Uses of Nylon-6
These include polymers like bakelite and melamine polymers.
i. Phenol formaldehyde resin (bakelite): These are prepared by the condensation reaction of phenol and formaldehyde in the presence of either an acid or a base catalyst. The reaction starts with the initial formation of o- and/or p-hydroxymethyl phenol derivatives, which further react with phenol to form compounds having rings joined to each other through \( – {\rm{CH2}}\) groups.
The initial product could be a linear product-Novolac used in paints. Novolac on heating with formaldehyde undergoes cross-linking to form an infusible solid mass called bakelite.
Uses of Bakelite
A high degree of polymerization results in the formation of hard bakelite, which is used to make combs, gramophone records, electrical switches, utensil handles, formica table tops, and many other products. Sulphonated bakelites are used as ion-exchange resins for hard water softening.
ii. Melamine Formaldehyde Polymer: Melamine and formaldehyde copolymerize to give melamine formaldehyde polymer.
Characteristics and Uses of Melamine Formaldehyde Polymer
Melamine polymer is a hard material that is used to make plastic crockery under the brand name Melmac. Melamine polymer cups, plates, and other items do not break when dropped.
The difference between addition polymerization and condensation polymerization is explained below.
Addition Polymerization | Condensation Polymerization |
Monomers must have a double or triple bond in this case. | Monomers in this case must have two functional groups that are either similar or dissimilar. |
There are no by-products produced. | Ammonia, water, and \({\rm{HCl}}\) are produced as by-products. |
Polymers are formed by the addition of monomers. | Polymers are formed by the condensation of monomers. |
The molecular of the is weight resulting in polymers is a multiple of the molecular weight of the monomer. | The molecular weight of the resulting polymer is not a multiple of the molecular weight of the monomer. |
Polymerization is the process of combining many small molecules known as monomers to form a covalently bonded chain or network. During the polymerization process, some chemical groups from each monomer may be lost. There are two types of polymerization: addition polymerization, also known as chain-growth polymerization, and condensation polymerization, also known as step-growth polymerization.
Q.1. What are the methods of Polymerization?
Ans: The methods of polymerization are addition polymerization and condensation polymerization.
Q.2. What are the two methods of polymerization?
Ans: The two methods of polymerization are addition polymerization and condensation polymerization.
Q.3. What are the three steps of radical polymerization?
Ans: There are three steps in this polymerization. These are Chain initiation, Chain propagation and chain termination.
Q.4. What are the two types of Polymerization?
Ans: There are two types of polymerization. They are chain-growth polymerization and step-growth polymerization.
Q.5. What is polymerization and its types?
Ans: Polymerization is the process of joining together many small molecules called monomers to form a covalently bonded chain or network. Types of polymerization are addition polymerization and condensation polymerization.
Q.6. What is the Classification Of Polymers?
Ans: Polymers are classified into the following types:
1. Classification based on the source of availability: Natural, synthetic and semi-synthetic polymers.
2. Classification based on structures: Linear, branched-chain and cross-linked polymers.
3. Classification based on molecular forces: Elastomers, fibres, thermoplastic and thermosetting plastic polymers.
4. Classification based on the mode of synthesis: Addition polymers and Condensation polymers.
Study Classification of Polymers Here
We hope this article on general methods of polymerisation has helped you. If you have any queries, drop a comment below and we will get back to you.