
Which of the following is incorrect about the zone refining?

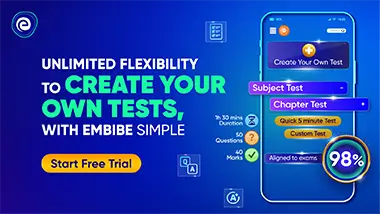
Important Points to Remember in Chapter -1 - General Principles and Processes of Isolation of Elements from Embibe Experts Gamma Question Bank for Engineering Chemistry Solutions
1. Minerals, Ores and Gangue:
The compound of a metal found in nature is called a mineral. The minerals from which metal can be economically and conveniently extracted are called ores. An ore is usually contaminated with earthy or undesired materials known as gangue.
Native ores contain the metal in free state. Silver, gold, platinum etc, occur as native ores.
Oxidised ores consist of oxides or oxysalts (e.g., carbonates, phosphates, sulphates and silicates) of metals.
Sulphurised ores consist of sulphides of metals like iron, lead, zinc, mercury etc.
Halide ores consist of halides of metals.
Metal | Ores | Composition |
---|---|---|
Aluminium | Bauxite | |
Diaspore | ||
Corundum | ||
Kaolinite (a form of clay) | ||
Iron | Haematite | |
Magnetite | ||
Siderite | ||
Iron pyrite | ||
limonite | ||
Copper | Copper pyrite | |
Copper glance | ||
Cuprite | ||
Malachite | ||
Azurite | ||
Zinc | Zinc blende or Sphalerite | |
Calamine | ||
Zincite | ||
Lead | Galena | |
Anglesite | ||
Cerussite | ||
Magnesium | Carnallite | |
Magnesite | ||
Dolomite | ||
Epsom salt (Epsomite) | ||
Langbeinite | ||
Tin | Cassiterite (Tin stone) | |
Silver | Silver glance (Argentite) | |
Chlorargyrite (Horn silver) |
2. Metallurgy:
The scientific and technological process used for the extraction/isolation of the metal from its ore is called as metallurgy.
(i) The isolation and extraction of metals from their ores involve the following major steps:
(a) Crushing and Grinding: The ore is first crushed by jaw crushers and grinded to a powder.
(b) Concentration: The removal of unwanted useless impurities from the ore is called dressing, concentration or benefaction of ore. The various methods for concentration of ores are:
Hydraulic washing or Gravity separation or Levigation method: It is based on the difference in the densities of the gangue and ore particles. This method is generally used for the concentration of oxide and native ores.
Electromagnetic separation: It is based on differences in magnetic properties of the ore components. Chromite ore is separated from non-magnetic silicious impurities and cassiterite ore is separated from magnetic Wolframite
Froth floatation process: This method is commonly used for the concentration of the low-grade sulphide ores like galena, (ore of ); copper pyrites
or (ore of copper); zinc blende, (ore of zinc) etc., and is based on the fact that gangue and ore particles have different degree of wettability with water and pine oil; the gangue particles are preferentially wetted by water while the ore particles are wetted by oil. In this process one or more chemical frothing agents are added.
Leaching: Leaching is often used if the ore is soluble in some suitable solvent, e.g., acids, bases and suitable chemical reagents.
(ii) Conversion into oxide:
(a) Calcination. It is a process of heating the concentrated ore strongly in limited supply of air or in the absence of air. The process of calcination brings about the following changes:
The carbonate ore gets decomposed to form the oxide of the metal.
Water of crystallisation present in the hydrated oxide ore gets lost as moisture.
Organic matter, if present in the ore, gets expelled and the ore becomes porous. Volatile impurities are removed.
(a) Roasting. It is a process of heating the concentrated ore (generally sulphide ore) strongly in the excess of air or below its melting point. Roasting is an exothermic process once started it does not require additional heating.
(iii) Reduction of ore.
(iv) Refining of ore.
3. Smelting:
Slag formation: In many extraction processes, an oxide is added deliberately to combine with other impurities and form a stable molten phase immiscible with molten metal called a slag. The process is termed smelting. The principle of slag formation is essentially the following:
Removal of unwanted basic and acidic oxides: For example, is the impurity in extraction of from copper pyrite.
Matte also contains a very small amount of iron (II) sulphide. To remove unwanted acidic impurities like sand and smelting is done in the presence of limestone.
(fusible slag)
(fusible slag - Thomas slag)
4. Reduction with carbon:
(extraction of lead)
Reduction with : In some cases, produced in the furnace itself is used as a reducing agent.
5. Reduction by other metals:
Metallic oxides ( and ) can be reduced by a highly electropositive metal such as aluminium that liberates a large amount of energy on oxidation to The process is known as Goldschmidt or aluminothermic process and the reaction is known as thermite reaction.
Magnesium reduction method: Magnesium is used in similar way to reduce oxides. In certain cases where the oxide is too stable to reduce, electropositive metals are used to reduce halides.
6. Self-reduction method:
This method is also called auto-reduction method or air reduction method. If the sulphide ore of some of the less electropositive metals like are heated in air, a part of these is changed into oxide or sulphate then that reacts with the remaining part of the sulphide ore to give its metal and .
7. Electrolytic reduction:
It presents the most powerful method of reduction and gives a very pure product. As it is an expensive method compared to chemical methods, it is used either for very reactive metals such as magnesium or aluminium or for production of samples of high purity.
(i) In aqueous solution: Electrolysis can be carried out conveniently and cheaply in aqueous solution that the products do not react with water. Copper and zinc are obtained by electrolysis of aqueous solution of their sulphates.
(ii) In fused melts: Aluminium is obtained by electrolysis of a fused mixture of and cryolite .
Extraction of Aluminium: It involves the following processes:
(a) Purification of bauxite:
(i) Bayer's Method (used for red bauxite containing and silicates as impurities) (insoluble) separated as red mud by filtration solution is diluted with water and seeded with freshly prepared It induces the precipitation of is filtered leaving behind silicates in solution |
(ii) Hall's Method (used for red bauxite containing ) |
(iii) Serpeck's Method (used for white bauxite containing silica as impurity) Silicone volatilises at this temp. |
(b) Electrolytic reduction (Hall-Heroult process):
Cathode:
Anode:
8. Metallurgy of Some Important Metals:
(i) Extraction of iron from ore haematite:
(a) Reactions involved:
At (lower temperature range in the blast furnace)
(higher temperature range in the blast furnace):
limestone is also decomposed tom which removes silicate impurity of the ore as slag. The slag is in molten state and separates out from iron.,
(ii) Extraction of copper:
From copper glance / copper pyrite (self-reduction):
,
(fusible slag)
(self-reduction)
(iii) Extraction of lead:
(iv) Extraction of zinc from zinc blende:
The ore is roasted in presence of excess of air at temperature .
The reduction of zinc oxide is done using coke.
(v) Extraction of tin from cassiterite:
The concentrated ore is subjected to the electromagnetic separation to remove magnetic impurity of Wolframite. is reduced to metal using carbon at in an electric furnace. The product often contains traces of , which is removed by blowing air through the molten mixture to oxidise which then floats to the surface.
(vi) Extraction of Magnesium:
From Sea water (Dow's process):
Sea water contains magnesium as chloride and sulphate. It involves following steps.
(a) Precipitation of magnesium as magnesium hydroxide by slaked lime.
(b) Preparation of hexahydrate of magnesium chloride.
The solution on concentration and crystallisation gives the crystals of
(c) Preparation of anhydrous magnesium chloride.
(d) Electrolysis of fused anhydrous in presence of .
At cathode:
At anode:
(vii) Extraction of gold and silver (MacArthur-Forrest cyanide process):
(a) From native ores: Extraction of gold and silver involves leaching the metal with
(b) From argentite ore:
9. Physical Methods:
(i) Liquation Process: This process is used for the purification of the metal, which itself is readily fusible, but the impurities present in it are not, used for the purification of and , and for removing from alloy.
(ii) Fractional Distillation Process: This process is used to purify those metals which themselves are volatile and the impurities in them are non-volatile and vice-versa. and are purified by this process.
(iii) Zone Refining Method (Fractional Crystallisation Method): This process is used when metals are required in very high purity, for specific application. For example, pure and are used in semiconductors Chemical methods.
10. Oxidative Refining:
This method is usually employed for refining metals like , etc. In this method the molten impure metal is subjected to oxidation by various ways.
11. Poling Process:
This process is used for the purification of copper and tin which contains the impurities of their own oxides.
12. Electrolytic Refining:
Some metals such as and are refined electrolytically.
13. Vapor Phase Refining:
(i) Extraction of Nickel (Mond's process): The sequence of reaction is
(ii) Van Arkel process: